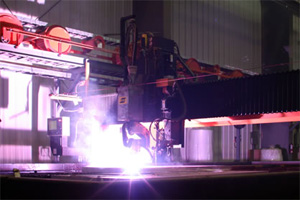
In today's precision cutting industry, plasma cutting machines are quite common. There are assortments of model types frequently used and all have specific sets of advantages and disadvantages.
The technology behind plasma cutters did not begin development until 1941 during the second World War. Researchers began looking for ways to to manufacture aircrafts with greater efficiency. The efforts resulted in what is called TIG or GTAW -- a welding process that employs an inert gas to pass through an electric arc. While this is the same method used in plasma cutters, is it not considered to be a plasma device, as it does not specifically use plasma to incise materials. Plasma was not introduced until the 1950's.
In 1954, with further research of the TIG and GTAW process, scientists realized a plasma jet could be created by decreasing the size of the nozzle opening while simultaneously increasing the speed of the gas flow.
Shielding gas channels and shielding gases began being incorporated with plasma machines in the 1960's. The technique had been introduced to reduce the effects of double arcing. Double arcing refers to the second electric arc that is often formed in plasma device. As a result, the main electric arc is moved to the outlet of the nozzle. While the use of a shielding as helped to alleviate double arcing, it did not fully eliminate the problem.
Looking at the stages of development for plasma devices through out history, several innovations have been established and researched to improve upon plasma systems, and to reduce its disadvantages. However, with every new model introduced, while it may have improved one aspect, it almost always highlighted a disadvantage, or created a new one. For instance, the Water Shield Plasma Cutter and the Oxygen Injection Plasma Cutter.
1965 introduced the Water Shield Plasma Cutter. This innovation made use of water to preform the same role as shielding gases. This change improved cut appearance and also expanded the nozzle life. However, it failed in areas of cut squareness, speed, and the amount of dross produced. Moreover, the water did not create any further additional arc constriction.
The Oxygen Injection Plasma Cutter was established in 1985. In this device, nitrogen gas is used as the inert gas to form plasma and oxygen is used to perform the task of the shielding gas. This alternative machine improved the life of the electrode and also increased the cutting speed rate. Unfortunately, it also eroded the nozzle part and thereby requiring frequent replacements. Additionally, it had poor cut squareness, produced unnecessary amounts of kerf removal, and could only work with mild steels.
From the 1990's and onward, air and oxygen have been the most common forms of plasma cutters used within the industry, in addition to computer numerical controlled options (CNC). A continuous problem for plasma systems are their consumable parts and short life spans. With more research, plasma machines are closer to improving the life expectancy of equipment, and as a result, improving upon performance and costs.